
Koenigsegg One:1 , (taken from www.flikr.com)
Koenigsegg, a Swedish supercar company founded by entrepreneur Christian Von Koenigsegg in 1994, is a fairly new company in comparison to its competition. What Koenigsegg lacks in racing pedigree, they outclass in technological innovations when it comes to the manufacturing of their cars. Since Koenigsegg is a relatively small car company which only produces a handful of automobiles each year, the trial and error methods of using cast manufacturing for the research, development, and production of parts becomes a costly process. Traditional cast manufacturing takes a lot of trial and error to make perfect but it is usually a very time consuming process. Because Koenigsegg doesn’t have their research and development expenses divided amongst a high volume of sales like Porsche, Ferrari, or McLaren, the company started exploring alternative production processes.
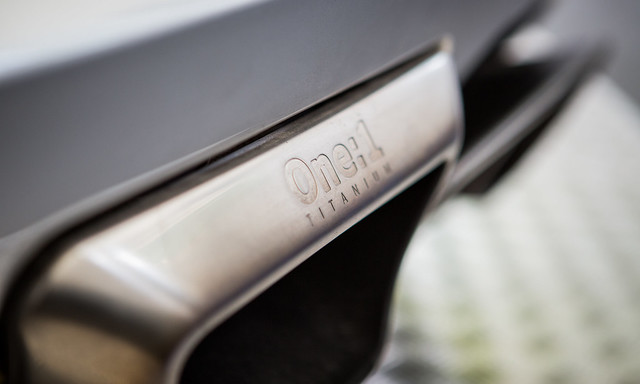
3D printed titanium exhaust port on the One:1 (photo taken from www.flikr.com)
In 2014 Koenigsegg launched the One:1, a car which featured many parts that the 3D printing process was used for. Because 3D printing enables engineers to calculate the dimensions of a part with ease on the computer, the trial and error methods of automobile manufacturing has made the research and development of parts much less expensive and time consuming. Although most of the parts that a 3D printer was used for on the One:1 were only for test fitting, advances in 3D printing technology has led to the printers being able to draft in metals like aluminum and titanium for some production pieces. Koenigsegg’s One:1 actually used the metal 3D printing process to create a complex type of turbocharger that would work more efficiently on the engine, a process which would have been very costly in terms of time and money using traditional casting methods.
Koenigsegg isn’t the only manufacturer to acknowledge the benefits of 3D printing in the auto industry. Nissan has been using 3D printing in their motorsports program and Mercedes-Benz has mentioned the possibility of using 3D printed parts in their interiors, while Opel has created custom 3D printed tools to aid in the assembly of cars on the manufacturing line. 3D printing is still a new technology and we have only discovered the tip of the iceberg in terms of its potential. The fact that these technologies being adopted by the automotive world at a rapid rate will eventually lead to the enhancements of 3D printing as well reduced manufacturing costs, which means a lower sticker price on new cars should be in store.